The Competence Industry Manufacturing 4.0 offers a specific training on technologies for the digitalization of the company and additive manufacturing starting from the training needs expressed by the companies: a real national reference of applied knowledge in Industry 4.0.
- Training drawn on real needs
- The educational offer: a national reference point
- Technological expertise paths
- Enterprise 4.0 Academy
- The virtual coach role
- Courses
Training drawn on real needs
The industrial culture 4.0 has as its pillars the continuous training and the knowledge of applied technologies, responding to the real needs of companies, from large to micro. Assessments, evidence of good practices or generalist training modules built on the new technological contents of Industry 4.0 are not enough: specific, in-depth training is required which, starting from the training needs expressed by the Companies proposes tailoring courses (gap of knowledge, skills and professional & managerial profiles).
The educational offer: a national reference point
To “hit the mark” and become a national reference of applied knowledge in Industry 4.0, we focused our training offer consistently with the strategic specificities of CIM4.0, that is, the technologies for the digitalization of the Company and additive manufacturing.
We have identified two complementary needs:
- Increase specialization on Industry 4.0 digital technologies
- Integrate the different technologies for the development of the company
We have defined two distinct training actions:
- Technological competence paths
- Enterprise 4.0 Academy
The training offer finalizes the skills and assets of the 23 Industrial Consortiums and the 2 Academies (University and Polytechnic of Turin) that carry out the role of scientific coordination, and it is mainly managed by specialist technicians of the consortium companies (senior specialist, technical fellow, senior technical fellow) and university professors.
In this way, CIM4.0 will support companies in the adaptation and / or development of skills, as well as in the creation of professional figures capable of promoting the continuous evolution of the product, technology and organization.
Technological expertise paths
The first training action allows to increase the technological competence in a progressive way from awareness, with introductory courses, to specialization applied with advanced courses or complete “tailoring” courses.
The training project will therefore be differentiated with respect to the subjects to be finalized internally or to be reconverted.
The training methods include classroom courses, e-learning, use of computer labs, activities at the pilot lines (Training On the Job).
The first courses, already planned, starting from December will concern the following areas: Data Science, Additive Manufacturing, World Class Manufacturing, Predictive Maintenance, Cyber Security, Methods and tools for digital transformation.
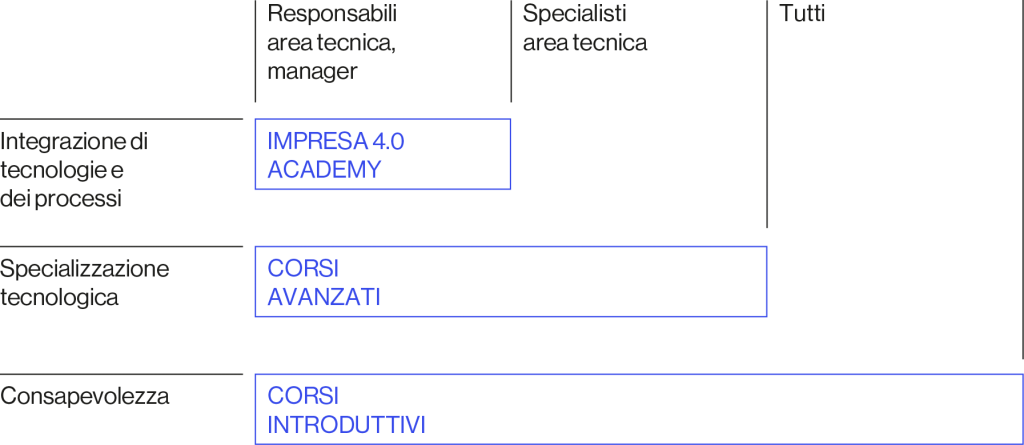
Enterprise 4.0 Academy
Regarding the school for managers of technical areas, or managers of the digital transformation; the training will consider a full-time or part-time period. The first part will be dedicated to achieve a specialized technological competence. The second part will be dedicated to the development of systemic skills, regarding technology and process integration as well as the evolution of the value chain, and managerial skills (Management and Business).
The approach used will be “challenge-based learning” and the real challenges will be identified by a team of business experts. The development is scheduled both at the CIM4.0 and at the structures of the consortium members.
The Virtual Coach® role
From next year, CIM4.0 Learning Hub’s training offer will make use of a digital platform and a VIRTUAL COACH® that combines Artificial Intelligence, Virtual Reality and Facial Expression Recognition, guiding the user in the training path (from selection to self-assessment).
This will allow at the same time flexibility of delivery, being able to access content at any time, and greater training effectiveness thanks to interactivity with the virtual tutor.
Coordinator
Cristina Cibrario
cristina.cibrario@cim40.com
Courses
List of courses divided by area
- All courses
- Predictive Maintenance
- Data Science
- WCM
- Additive Manufacturing
- Methods and tools for digital transformation
- Cyber Security