The all-Italian 4.0 supply chain for the production of masks
Published on April 19, 2025
CIM 4.0 has built, together with innovative small and medium-sized companies, an automated and digitized pilot line to test Innovations 4.0 and increasingly environmentally sustainable materials and define standard specifications to replicate at other companies the line for the production of Surgical Masks intended for business and the community.
This pilot line will enable the implementation and testing of innovative technologies and increasingly eco-friendly materials and the replication of automated Personal Protective Equipment production lines at other companies. It is based on modular systems that minimize specific investment costs and “open” componentry to enable hardware and software improvements and testing of innovative 4.0 solutions by companies and start-ups in the Italian ecosystem. The production process allows for 80 parts per minute and can be H24 continuous cycle.
Partners
All this has been achieved thanks to the active collaboration of the CIM 4.0 consortium members and the involvement of innovative SMEs: TECNOCAD, a leader in design and in charge of production; NICMA Group , a leader in the sale and distribution of personal protective equipment, which will be in charge of the dissemination of the masks; and ICRE , a leader for more than 50 years in the installation and automation of production lines, which is already working to replicate this initiative.
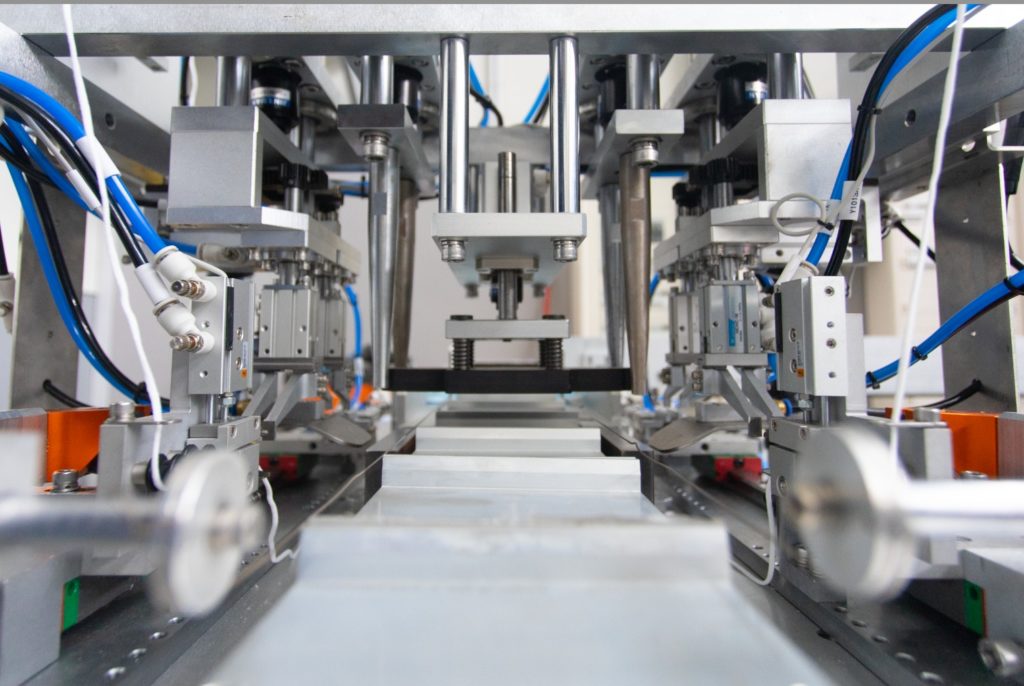
Everything was carried out quickly without neglecting any detail: from the choice of suppliers of raw materials, strictly Italian companies identified thanks to the scouting of CIM 4.0 and the Polytechnic University of Turin, and subsequently carried out by TECNOCAD, to the production and certification of the product, from the distribution of the templates, to the end-of-life management and recycling of materials.
What are the features that make this new line truly 4.0?
- Application of World Class Manufacturing principles, which ensure maximum productivity, total worker safety and ergonomics, and minimization of waste and energy consumption
- Real-time monitoring and remote control of the production process, in order to ensure the highest possible production efficiency and early detection of anomalies, including through predictive maintenance logic aimed at minimizing downtime
- Implementation of Digital Twinning of the line in order to simulate operational and calibration activities and enable optimization of production KPIs (Key Performance Indicators)
Our goal is to put 4.0 skills and methodologies aimed at technology transfer at the service of the country and, of course, the region in which we operate. This is the strategy we followed to realize this pilot line as well: a traditional industrial production process made digital and smart, thanks to our contribution and that of important industrial partners, aimed at producing in Italy a commodity needed to fight the spread of the virus. A concrete and timely demonstration of how expertise, technology, teamwork and a systemic approach can enable operations that are synergistic and at the same time functional to the real needs of the community and the economic development of production chains.
Enrico Pisino, CEO CIM4.0
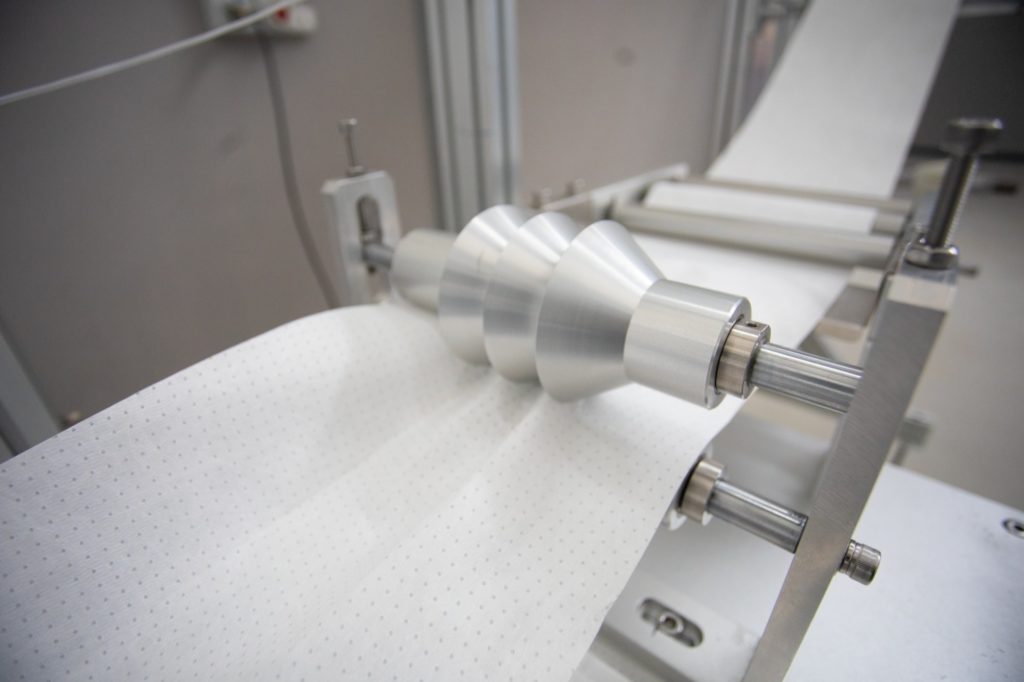